Governments around the world want to end the sale of petrol and diesel cars in the coming years, some as soon as 2030. Accordingly, market research specialist Statista, expects revenue in the electric vehicle market to show an impressive annual growth rate (CAGR) of 17.02% in the next four years, resulting in a projected market volume of $858 billion by 2027.
Faced with these predictions, not just automotive companies, but also various transportation industries, are understandably busy implementing their biggest operational changes in decades, an activity that presents a number of e-powertrain design challenges. For most automotive engineers, e-powertrain technologies represent new territory that demand considerable resources and time to create safe and efficient solutions. It is here that silicon carbide (SiC) can deliver major advantages.
The elephant in the room for EV technology is of course range anxiety. While much of the focus here is on battery capacity, the drivetrain and automotive system electronics must also prove highly efficient and capable of high power-optimal performance under demanding conditions. This is why SiC is capturing attention, as acknowledged by a number of leading authorities. The UK?s Advanced Propulsion Centre, for example, says that switching from silicon to silicon carbide-based power electronics could offer an efficiency gain of approximately 10%.
The attributes of SiC also enable designers to create power systems with considerable reductions in size, weight and form-factor. Despite all the benefits, engineers should note that designing with SiC is different to using conventional silicon MOSFETs or IGBTs. Most of the nuances involve the use of special technologies that facilitate safe operation at high-speed switching.
To reduce the cost of engineering resources and to shorten time-to-market, there is a need for fully integrated solutions. CISSOID?s SiC traction-inverter development platform meets this demand supporting the design of drive systems up to 850V/350kW. The core components of this reference design include: a 3-phase 1200V intelligent power module (IPM) with powerful and temperature-robust gate driver fully optimised for SiC application; an e-motor control board and customisable software; DC and phase current sensors, a compact liquid cooler; a specially designed high-density DC-link capacitor and EMI filtering.
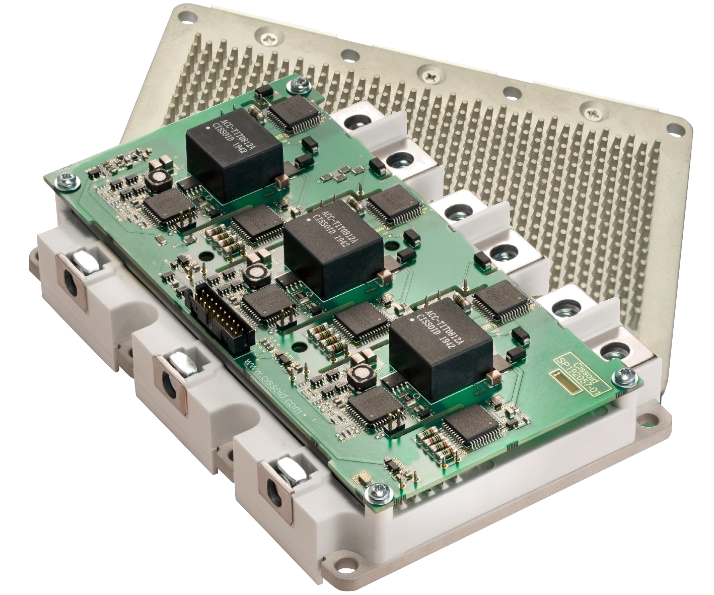
Each of these drop-in building blocks has a vital role to play in providing the comprehensive capability and modularity of the platform.
CISSOID?s 3-phase, liquid-cooled, 1200V SiC MOFSET IPM (Figure 2) gives access to the full benefits of SiC technology, helping developers to achieve high power density thanks to low switching losses and high-temperature operation. Bringing modularity to changing voltage/current requirements, CISSOID?s SiC IPM portfolio consists of modules with maximum continuous current capability from 340A to 550A. Comprising three silicon carbide MOSFET half bridges, the IPM reduces switching losses by at least a factor of three compared with state-of-the-art IGBT power modules.
To take full advantage of fast switching and low-loss SiC MOSFETs, engineers need a fast, powerful and robust gate driver. Integrating a gate driver with a power module provides direct access to a fully validated and optimised solution regarding switching speed and losses, robustness against dI/dt and dV/dt, and protection of the power stages.
CISSOID?s optimised gate driver provides high peak current, more than 10A, while also delivering operational capability up to 125°C ambient. In short, the optimised gate driver helps to minimise the number of iterations required to deliver perfect module performance and thermal management.
The capability of SiC power modules to switch faster and operate at higher frequencies makes it essential to access controller technology that can run real-time algorithms faster.
Based on the Silicon Mobility OLEA? T222 FPCU, CISSOID developed a board that delivers real-time processing, control and functional safety (ISO 26262 ASIL-D ready) for automotive motor control applications. The control hardware and software effectively process signals from motor position, current and temperature sensors. Notably, mechanical and electrical integration between the control board and IPMs removes another hurdle from the developer?s path.
The platform integrates with Silicon Mobility?s OLEA APP INVERTER control software (Figure 3), while engineers can use OLEA COMPOSER design tools to shorten the time required to develop and optimise the motor control software.

There are two more design points of note. Firstly, CISSOID offers a 3D-printed cooler reference design for cooling and rapid evaluation of the power module (Figure 4). Secondly, the company has collaborated with NAC Semi and Advanced Conversion to create a high-density DC-link capacitor with very low inductance and ESR that provides developers with full freedom to leverage the fast-switching capability of SiC MOSFETs.
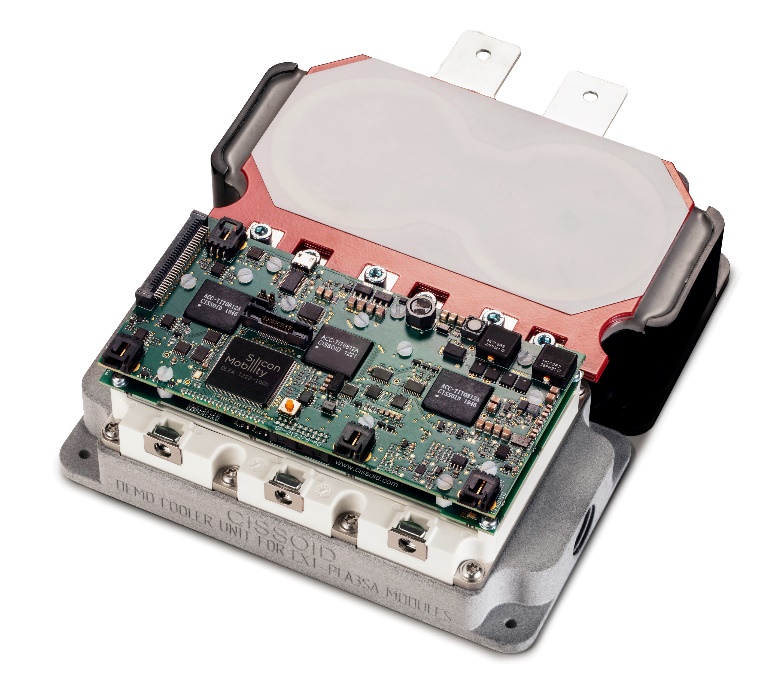
Ultimately, CISSOID?s unique hardware and software modular platform makes it possible to develop highly compact, efficient and critically safe SiC-based traction inverters or active rectifiers in only a few months. Set against conventional OEM timelines, this can save between one and two years in SiC inverter development.