W branży produkcyjnej jedno jest pewne ? jeśli ktoś stoi w miejscu, zostanie prześcignięty. Fabryki wymagają elastyczności, dzięki której mogą stale zwiększać wydajność i wprowadzać nowe lub ulepszone produkty.
Producenci muszą nieustannie dostosowywać się, aby podnosić produktywność i wydajność produkcji, najlepiej przy minimalnym zakłóceniu działalności. Niektóre z rozwiązań, takie jak modernizacja maszyn czy instalacja dodatkowych linii produkcyjnych, są zazwyczaj możliwe jedynie w rzadkich odstępach czasu. Pomiędzy poważniejszymi inwestycjami tego rodzaju, w celu podniesienia wydajności niezbędne jest wprowadzanie usprawnień konfiguracji procesów oraz praktyk, na przykład odnośnie procedur przestawiania linii produkcyjnych.
Wdrażanie zasad ciągłego doskonalenia
Aby zwiększyć wydajność, pewien japoński producent części samochodowych próbował skrócić czas cykli przy najważniejszych procesach, zwiększając jednocześnie prędkość przenośnika, aby skrócić do minimum czas przemieszczania poszczególnych elementów między procesami. Zespół produkcyjny tej firmy stwierdził, że zwiększanie prędkości powyżej określonego poziomu przynosi coraz mniejsze korzyści. Jeżeli szybko poruszające się elementy są zatrzymywane za pomocą konwencjonalnego pneumatycznego siłownika zatrzymującego, potrzeba istotnie więcej czasu na zatrzymanie obrabianego elementu, zanim można go ściągnąć z przenośnika i włączyć do procesu. Stwierdzono również, że zwiększenie prędkości maszyn procesowych w celu osiągnięcia szybszego tempa cyklu prowadzi do częstszych przestojów linii w celu usunięcia błędów urządzeń.
Inny producent wytwarzający małe silniki elektryczne, starał się w sposób bardziej efektywny realizować zamówienia na krótkie serie określonych wariantów produktów poprzez skrócenie czasu przestawiania linii. Optymalizacja procedur przestawiania pozwoliła skrócić ten czas o 50%, z 10 do 5 minut. Jednak skumulowany efekt tych pięciominutowych zmian, dokonywanych zazwyczaj kilka razy dziennie, oznaczałby stratę około 16 godzin pracy w skali miesiąca. Aby zoptymalizować wydajność, zespół był zmuszony zatem uważnie zarządzać produkcją, nadając pierwszeństwo produktom wytwarzanym w największej ilości.
Aby uniknąć straty czasu, firma próbowała opracować specjalny przyrząd do produkcji różnych wariantów produktu bez konieczności rekonfiguracji linii. Ten niestandardowy przyrząd, przystosowany do mocowania trzech rodzajów komponentów w małym, średnim i dużym rozmiarze, umożliwił linii obróbkę nawet dziewięciu różnych wariantów produktu bez konieczności przestawiania linii. Jednak dwuosiowy robot wykorzystywany do usuwania wybranego elementu z odpowiedniej pozycji w przyrządzie wymagałby zmiany pozycji zatrzymania przenośnika w zależności od wytwarzanego wariantu produktu (rys. 1). Alternatywnie, zastąpienie robota dwuosiowego modelem trzyosiowym umożliwiłoby robotowi przemieszczanie się wzdłuż przyrządu, tak aby wybrać odpowiedni element. Każde z tych rozwiązań wiąże się z dodatkowymi kosztami i utratą części oczekiwanych oszczędności pod względem czasu produkcji.
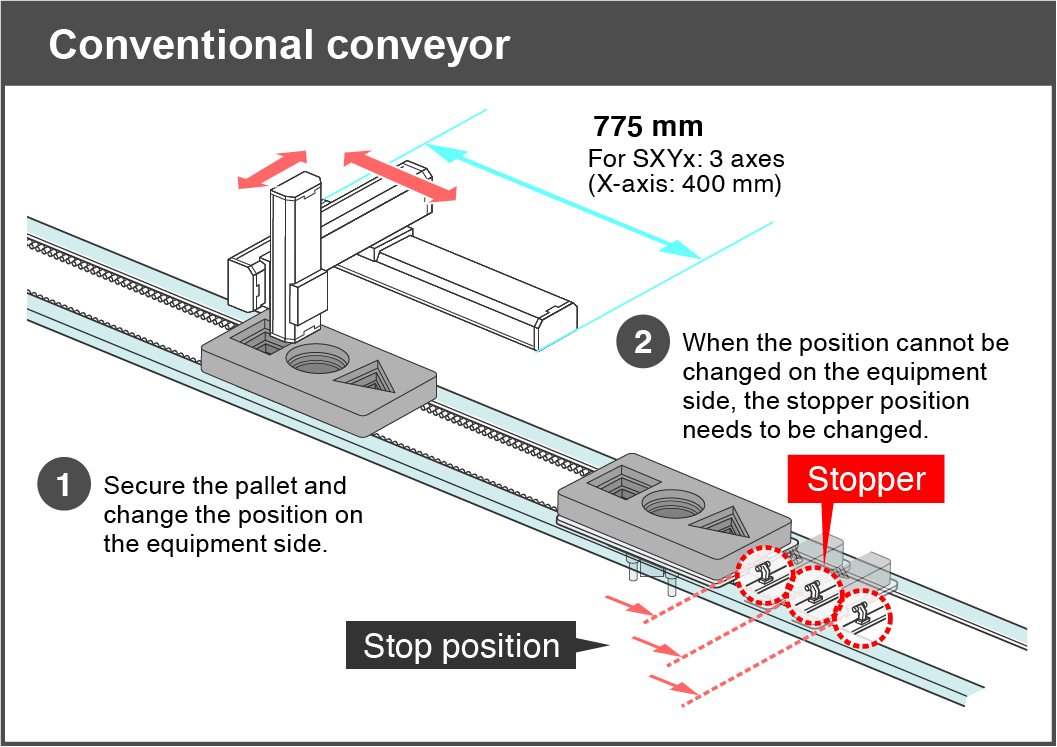
Projektowanie i obsługa systemu przenośnikowego
Inteligentnie zaprojektowany system przenośników, który jest główną arterią biegnącą przez linię produkcyjną, może pomóc zmaksymalizować wydajność produkcji, wyeliminować ręczną obsługę i optymalne wykorzystać przestrzeń fabryczną. Konfiguracja systemu przenośników w celu optymalizacji pracy zakładu jest umiejętnością, która często polega na dostosowaniu standardowych urządzeń dostępnych na rynku lub opracowaniu indywidualnych rozwiązań dla konkretnych wymagań środowiska fabrycznego, takich jak skrajne ograniczenia przestrzenne lub różnice poziomów. Często wymagane są jednostki buforowe, które pozwalają na dostosowanie się do różnic wydajności maszyn pracujących w danej linii i umożliwiają jej spójne, skoordynowane działanie. Producenci systemów przenośnikowych oferują wiele różnych opcji i konfiguracji, a nawet specjalne autorskie produkty, które są w stanie sprostać indywidualnym potrzebom klientów.
Ze względu na to, że system jest zazwyczaj projektowany przez specjalistów na podstawie wytycznych, wynik jest ściśle dopasowany do potrzeb fabryki, określonych przy rozpoczęciu projektu. W miarę zmian i ewolucji tych wymagań, dokonywanie odpowiednich modyfikacji systemu transportowego może sprawiać trudności. Na przykład zmiana pozycji zatrzymania za pomocą siłowników pneumatycznych oraz związanych z nimi czujników i zaworów elektromagnetycznych może wiązać się z koniecznością wprowadzania obszernych zmian w oprogramowaniu, okablowaniu i nastawie mechanicznej.
Na takie ograniczenia natknęły się obie firmy produkujące części samochodowe i małe silniki, gdy próbowały zwiększyć wydajność produkcji przy użyciu konwencjonalnych przenośników. W obu przypadkach zespoły projektowe nie zdołały osiągnąć 100 procent pożądanej optymalizacji.
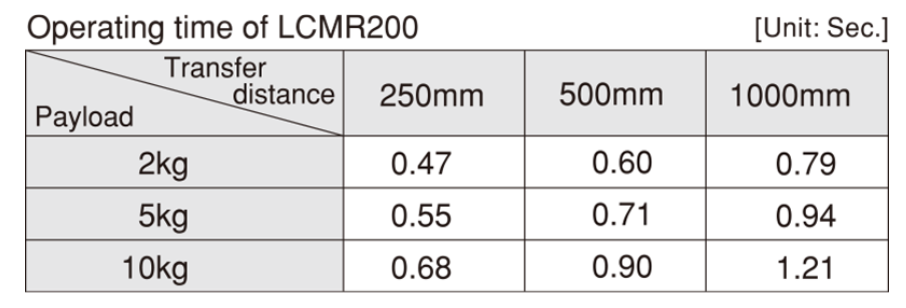
Transport obrabianych elementów za pomocą modułów liniowych
Moduł przenośnika liniowego LCMR200 firmy Yamaha pozwala na znacznie większą elastyczność w dostosowaniu i poprawie wydajności linii produkcyjnej w porównaniu z konwencjonalnymi przenośnikami. Parametry takie jak przyspieszenie, zwolnienie, prędkość i pozycje zatrzymania są ustawiane elektronicznie i łatwo regulowane poprzez wprowadzenie nowych, oczekiwanych wartości do sterownika. Dodatkowo, silnik liniowy umożliwia ruch w dwóch kierunkach.
Powiązany sterownik YHX eliminuje konieczność pisania drabinkowych kodów logicznych ? pozwala on użytkownikowi na określenie bezpośrednich wartości i prostych ruchów z punktu do punktu. Jeden sterownik może koordynować wiele modułów LCMR200 połączonych ze sobą jako elementy kompletnej komórki produkcyjnej.
Ponieważ do dodania dodatkowych pozycji zatrzymania nie są potrzebne żadne dodatkowe czujniki, użytkownicy mogą łatwo rekonfigurować swoją linię produkcyjną bez utraty niezawodności. Silnik liniowy przyspiesza oraz zatrzymuje się szybko i płynnie, a czas stabilizacji po dotarciu do żądanej pozycji może być bardzo krótki. W praktyce czas stabilizacji można zoptymalizować regulując tolerancję pozycjonowania: większa tolerancja pozwala na skrócenie czasu stabilizacji. Co więcej, użytkownik może zwiększyć prędkość przenośnika bez konieczności wprowadzania dodatkowego buforowania, ponieważ każdy moduł ma możliwość niezależnego zatrzymania, ponownego uruchomienia i cofnięcia, co pozwala na dostarczenie każdego elementu w optymalnym czasie.
Przesuwnik LCMR200 można zaprogramować tak, aby zatrzymywał się w dowolnym miejscu, z maksymalną powtarzalnością pozycjonowania rzędu ?5 ?m. Prędkość transferu jest natomiast regulowana elektronicznie do 2500 mm/s. Poniższa tabela porównuje typowe czasy potrzebne do przeniesienia detali, w zależności od obciążenia użytkowego.
Przesuwnik może przenosić obciążenia do 15 kg, a sztywność modułu pozwala na dokonywanie obróbki bez zdejmowania elementu z przesuwnika (rys. 2). Zapewnia to szybki czas cyklu, a także pozwala ograniczyć nakład pracy inżynierów oraz koszty związane z opracowaniem mechanizmu przenoszenia obrabianego elementu do i z osobnego przyrządu przy każdym procesie.
Wspomniany wcześniej producent części samochodowych szybko przekonał się, jak LCMR200 może pomóc w osiągnięciu 100 procent pożądanej poprawy wydajności. W ramach projektu pilotażowego, przeprojektowanie jednej z linii produkcyjnych w celu zastąpienia konwencjonalnych przenośników modułami LCMR200 pozwoliło na znaczne skrócenie czasu transferu. Ta oszczędność czasu z kolei zmniejszyła presję na skrócenie czasu cyklu różnych procesów w linii. W rezultacie wolumen produkcji przekroczył pierwotnie zakładany przez zespół cel, a liczba błędów prowadzących do przestojów zmniejszyła się do tego stopnia, że ta linia montażowa zyskała miano wzorcowej w zakładzie.
Także producent silników elektrycznych wykorzystał LCMR200 do zwiększenia wydajności poprzez zwiększenie elastyczności linii produkcyjnej. Możliwość zmiany pozycji zatrzymania modułu poprzez przeprogramowanie pozwoliła na zaoszczędzenie sporej ilości pracy ręcznej przy konfiguracji. Następnie zespół wprowadził czytnik kodów QR do identyfikacji każdego typu urządzenia na początku produkcji, aby umożliwić wszystkim modułom LCMR200 automatyczną rekonfigurację ustawień. Dzięki temu wyeliminowano konieczność interakcji człowieka z maszynami lub urządzeniami za pomocą panelu dotykowego, co pozwoliło na pełną, kompleksową automatyzację montażu produktów. Dzięki temu znacznie wzrosła wydajność pracy i wyeliminowano konieczność interwencji operatora przy zmianie modelu produktu. Firma może teraz realizować krótkie serie produkcyjne równie sprawnie jak największe zamówienia.
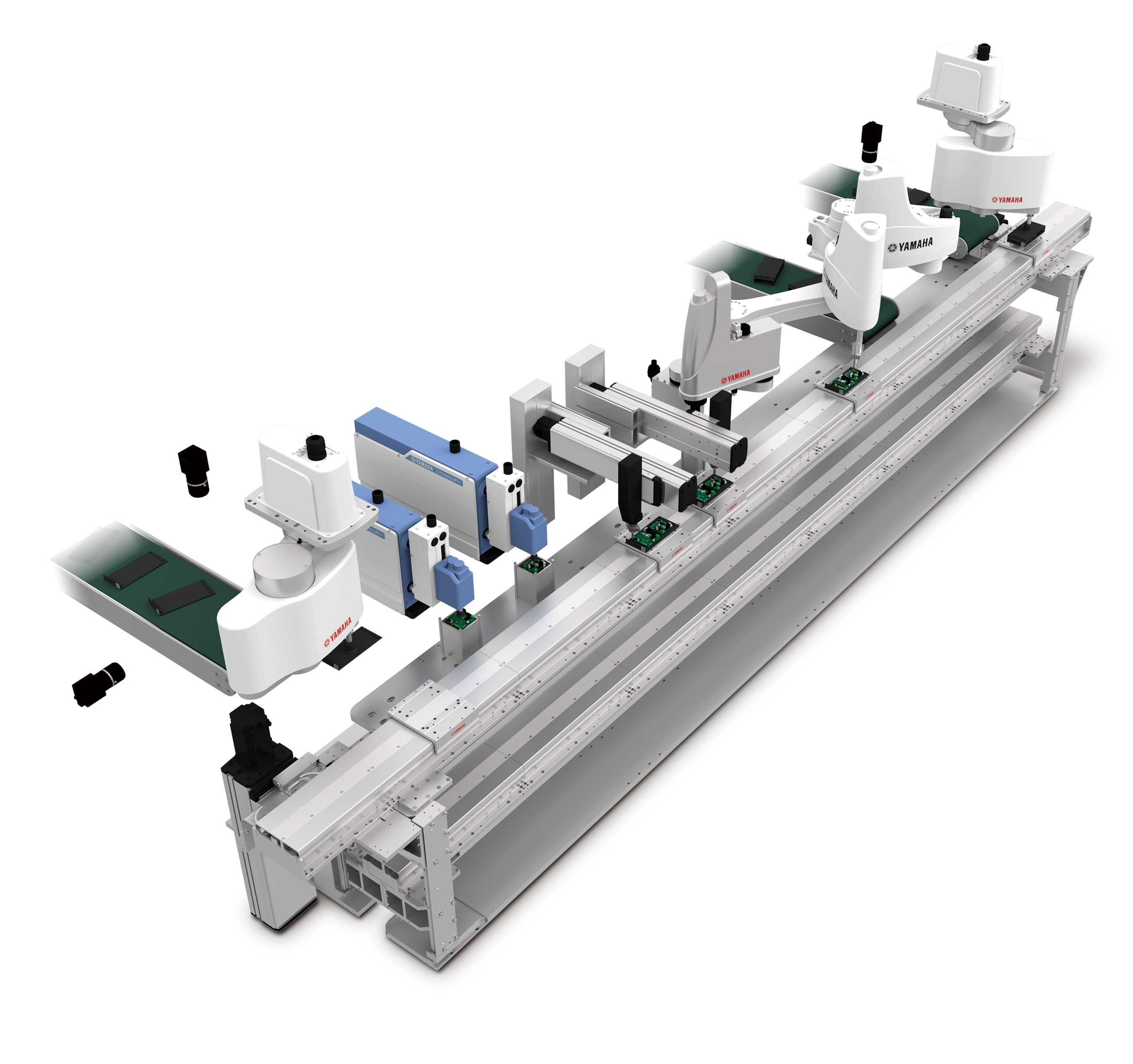
Podsumowanie
Przedsiębiorstwa produkcyjne są stale poddawane presji zwiększania wydajności poprzez zwiększanie prędkości linii i skracanie czasu przestawiania. Konwencjonalne przenośniki mogą stać na przeszkodzie rozwojowi, ponieważ oferują jedynie ograniczoną elastyczność, zaś ich rekonfiguracja wymaga dużego nakładu pracy inżynierów. Często nie daje się uzyskać wymaganej poprawy poprzez wprowadzenie prostych zmian. Z drugiej strony, dokonywanie poważniejszych zmian wymaga zazwyczaj istotnego wsparcia ze strony partnera handlowego.
Dwukierunkowe moduły przenośników liniowych umożliwiają wszechstronną rekonfigurację parametrów, takich jak prędkość i pozycje zatrzymania. Co więcej, właściciele urządzeń mogą zazwyczaj samodzielnie dokonywać tych zmian. Dodatkowe korzyści to możliwość przeprowadzania procesów takich jak montaż mechaniczny bezpośrednio na module, co pozwala na oszczędność czasu procesu oraz nakładów technicznych związanych ze zdejmowaniem i zastępowaniem elementu na konwencjonalnym przenośniku.
Yamaha Factory Automation Section (Sekcja FA) to pododdział Yamaha Motor Robotics Business Unit w Yamaha Motor Corporation. Zajmuje się dostarczaniem elastycznych, wysoce precyzyjnych robotów przemysłowych, które spełniają wymogi precyzyjnej automatyzacji.